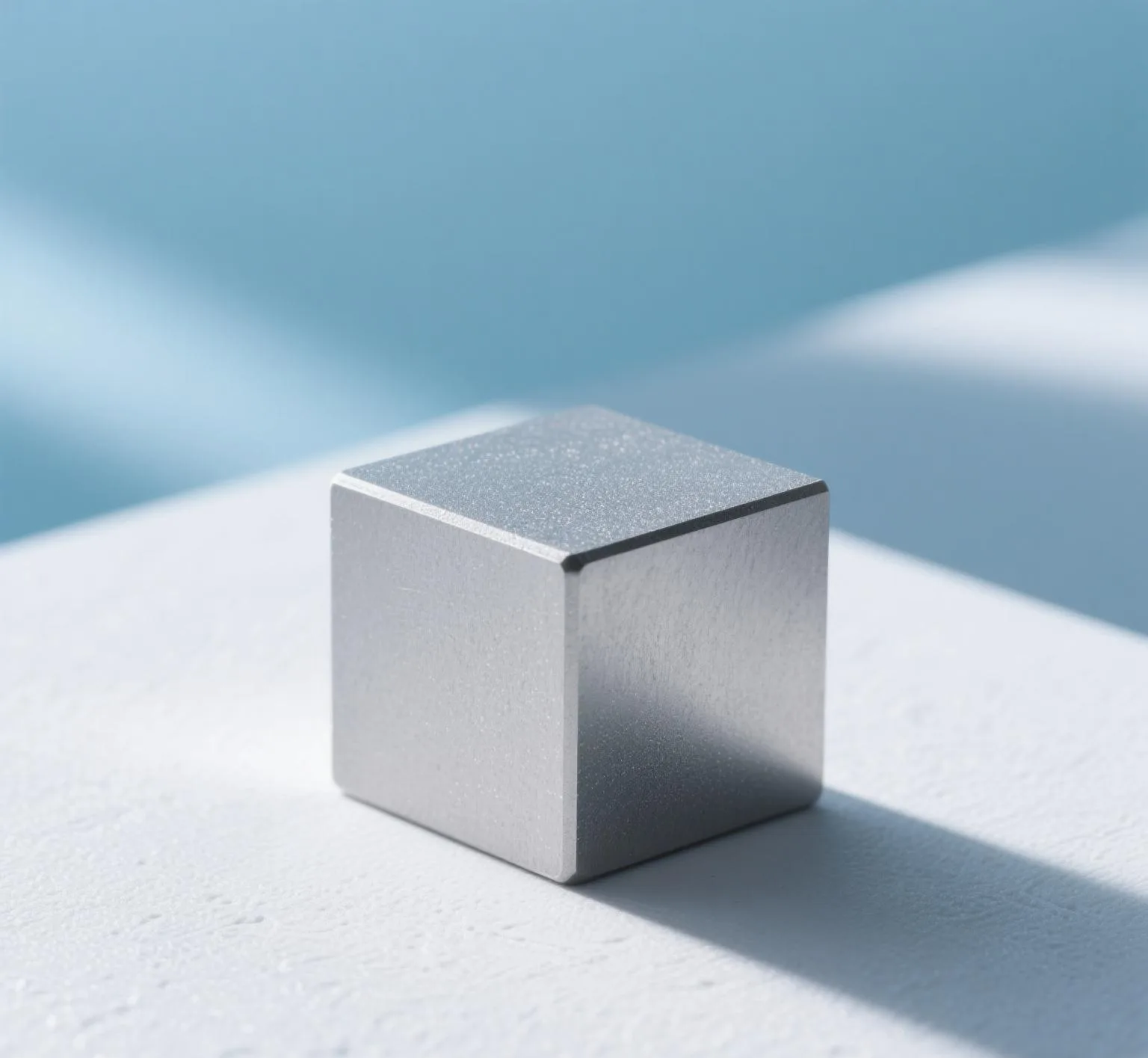
What Is Niobium Smelting?
Niobium smelting is the process of extracting and refining niobium (Nb) from its ores, primarily pyrochlore and columbite. This rare metal, prized for its heat resistance and superconductivity, undergoes a series of steps—crushing, chemical leaching, and high-temperature reduction—to become pure niobium or niobium alloys. Think of it as transforming raw ore into the backbone of aerospace alloys, superconductors, and advanced ceramics.
Why Is Smelting Niobium So Important?
Niobium’s unique properties make it irreplaceable in modern tech:
- Superconductivity: Enables MRI machines and particle accelerators.
- Heat Resistance: Withstands 2,468°C, critical for jet engines.
- Corrosion Immunity: Perfect for chemical reactors and implants.
Without smelting, we couldn’t unlock these traits.
How Is Niobium Smelted? Step by Step
- Ore Processing: Crushed ore is treated with hydrofluoric acid to extract niobium oxide (Nb₂O₅).
- Reduction: In electric arc furnaces, Nb₂O₅ reacts with carbon or aluminum at 1,500°C to produce niobium metal.
- Refining: Electrolysis or electron beam melting removes impurities like tantalum (Ta), ensuring 99.9% purity.
- Alloying: Smelted niobium is blended with metals (e.g., titanium) or carbon (for carbides like FTNC alloys in GB/T 26061-2010).
Key Fact: Smelting defines final properties—grain size, oxygen content (<0.3% for high-grade niobium), and strength.
Where Does Smelted Niobium Go?
- Aerospace: Jet turbine blades and rocket nozzles.
- Medical: MRI magnet coils and biocompatible implants.
- Energy: Superconducting wires for fusion reactors (learn more at ITER).
- Hardware: Niobium carbide (NbC) in ultra-durable cutting tools.
For industry insights, explore the Niobium Institute.
For more information about the products of tantalum and niobium, please visit our product page:http://zzhytanb.com/services/