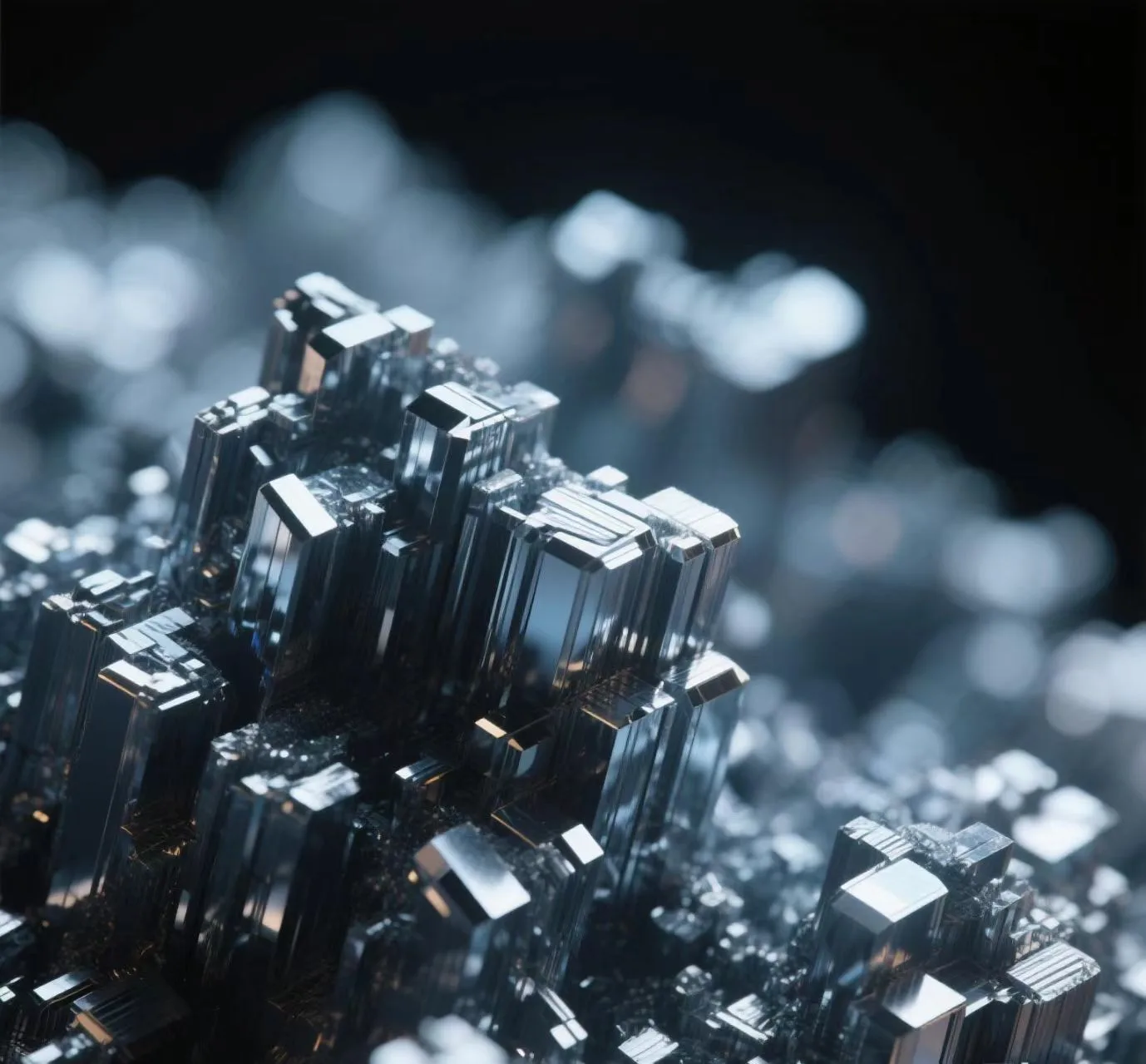
What Is Tantalum-Niobium Composite Carbide?
Tantalum-niobium composite carbide (TNCC) is a cutting-edge ceramic alloy formed by combining tantalum carbide (TaC) and niobium carbide (NbC). Governed by standards like GB/T 26061-2010, this material is engineered through a carbon thermal reduction process—where tantalum pentoxide (Ta₂O₅) or niobium oxide (Nb₂O₅) reacts with carbon at ultra-high temperatures. The result? A super-hard, heat-resistant compound tailored for extreme industrial demands.
Key Fact: TNCC isn’t a single material but a customizable family. For example:
- FTNC90/10: 84% tantalum, 9% niobium.
- FTNC20/80: 18.5% tantalum, 71% niobium.
These ratios let engineers fine-tune properties like hardness, melting point, and corrosion resistance.
How Is Tantalum-Niobium Carbide Produced?
The production follows strict steps to ensure precision:
- Raw Material Refining: Tantalum/niobium oxides are purified to remove impurities.
- Carbon Thermal Reduction: Heated with carbon at ~1,800°C, forming TaC/NbC grains.
- Particle Control: Final products are classified into A (≤1.0 µm), B (1.0–1.5 µm), or C (1.5–3.0 µm) grades based on particle size (FSSS method).
- Quality Checks: Oxygen content is capped at 0.3% (Grade A) to prevent brittleness.
Why Precision Matters: Even minor deviations in particle size or oxygen levels can weaken tools or coatings.
Why Should Industries Care About TNCC?
Here’s what makes TNCC indispensable:
- Unmatched Hardness: Rivals diamonds (up to 2,500 HV), perfect for cutting tools that slice through steel.
- Extreme Heat Resistance: Withstands temperatures over 2,000°C, crucial for rocket nozzles and turbine blades.
- Corrosion Immunity: Resists acids, alkalis, and molten metals, ideal for chemical reactors.
- Radiation Shielding: Absorbs neutrons, making it vital in nuclear reactors.
Case Study: TNCC-coated drill bits last 3x longer in oil/gas drilling compared to tungsten carbide.
Where Is TNCC Used Today?
- Mining & Drilling:
- Drill bits, crusher plates, and wear-resistant liners.
- Reduces downtime in harsh environments like deep-sea mining.
- Aerospace:
- Thermal barrier coatings for jet engines.
- Satellite components exposed to solar radiation.
- Electronics:
- High-voltage capacitors (learn more at KEMET Electronics).
- Semiconductor manufacturing tools.
- Nuclear Energy:
- Fuel rod cladding and reactor core shields.
- Check out the World Nuclear Association for nuclear material trends.
The Future of TNCC
Researchers are pushing boundaries:
- Additive Manufacturing: 3D-printing TNCC parts for custom geometries.
- Nanostructured Blends: Enhancing toughness for medical implants.
- Green Production: Recycling scrap carbide to reduce costs and environmental impact.
For more information about the products of tantalum and niobium, please visit our product page:http://zzhytanb.com/services/