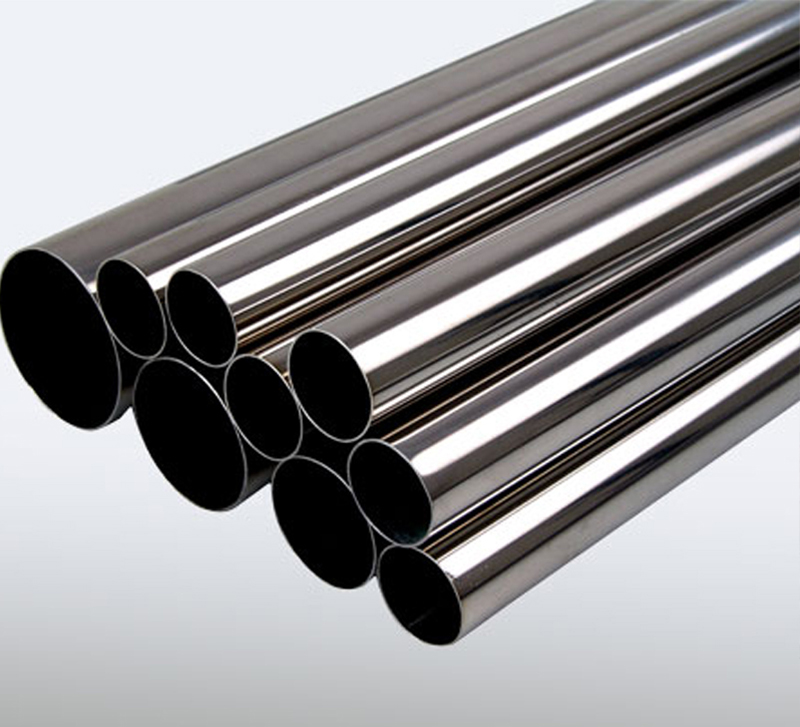
Tantalum Tubes: The Unsung Heroes of Corrosion Resistance and High-Performance Engineering
In industries where failure is not an option—chemical processing, aerospace, and medical implants—tantalum tubes are quietly revolutionizing reliability. As a material engineer fascinated by advanced metals, I’m breaking down why tantalum tubes deserve a spotlight in high-stakes applications.
Why Tantalum? The Metallurgical Edge
Tantalum’s unique properties make it irreplaceable in critical environments:
- Unmatched Corrosion Resistance: Resists virtually all acids (even boiling aqua regia and sulfuric acid), outperforming stainless steel and titanium.
- Biocompatibility: Ideal for surgical implants and pharmaceutical equipment due to non-reactivity with bodily fluids.
- High-Temperature Stability: Maintains structural integrity up to 3,000°C, crucial for aerospace and nuclear systems.
- Ductility: Can be drawn into ultra-thin tubes (wall thickness <0.1mm) without sacrificing strength.
Where Tantalum Tubes Excel
- Chemical Processing
- Lining reactors, heat exchangers, and piping systems handling aggressive acids.
- Reduces downtime caused by corrosion-induced failures.
- Medical Technology
- Used in bone repair meshes, drug delivery catheters, and MRI-compatible surgical tools.
- Meets ISO 10993 biocompatibility standards.
- Aerospace & Energy
- Fuel injection systems in rockets.
- Cladding for nuclear reactor control rods.
- Semiconductor Manufacturing
- Corrosion-resistant chambers for etching and CVD processes.
Manufacturing Precision Matters
High-quality tantalum tubes require strict adherence to standards like ASTM B521:
- Purity: ≥99.95% Ta, with controlled impurities (e.g., <50ppm oxygen).
- Dimensional Tolerance: Outer diameter ±0.05mm, wall thickness ±0.01mm.
- Testing: Hydrostatic pressure tests, ultrasonic flaw detection, and metallographic analysis.
The Innovation Frontier
- Additive Manufacturing: 3D-printed tantalum lattice structures for custom medical implants.
- Hybrid Coatings: Tantalum-clad steel tubes reduce costs while maintaining performance.
- Sustainability: Closed-loop recycling of machining scraps (up to 95% recovery rate).
A Challenge for Engineers
While tantalum tubes offer unparalleled performance, their high cost (~$500/kg) demands strategic use. How are you balancing performance and budget in corrosive environments? Have you explored hybrid solutions like tantalum-lined steel? Share your experiences below!
MaterialsScience #AdvancedManufacturing #CorrosionControl #EngineeringExcellence
Word Count: ~500 | Focus: Actionable insights for engineers, real-world applications, engagement hooks.
Tailored for LinkedIn’s professional audience—ready to post or refine further!