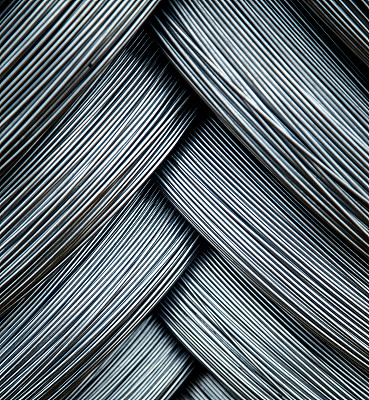
Tantalum Wire: The Hidden Backbone of High-Performance Capacitors
Meta Description
Discover how tantalum wire ensures reliability in capacitors. Learn about its grades, key properties, and how to choose the right wire for your electronic applications.
Why Tantalum Wire Is Your Best Choice for Capacitors
If you’re designing or sourcing components for electronics, tantalum wire (Ta wire) is a critical material you can’t overlook. Used in everything from smartphones to aerospace systems, this wire ensures capacitors deliver stable performance under extreme conditions. But what makes it so unique? Let’s explore.
1. Tantalum Wire Grades: DTa1 vs. DTa2 – Which Do You Need?
According to China’s GB/T 26012-2010 standard, tantalum wires are classified into two primary grades:
- DTa1: Pure tantalum (99.95% Ta) for general-purpose capacitors.
- DTa2: Doped tantalum with enhanced mechanical strength for high-stress environments.
Both grades come in three states:
- Soft (M): Ideal for intricate winding (e.g., miniature capacitors).
- Half-Hard (Y₂): Balances flexibility and strength.
- Hard (Y): Used where rigidity is critical (e.g., high-voltage systems).
Pro Tip: For liquid tantalum capacitors, opt for LDTa1/LDTa2 wires (0.4–0.8 mm diameter) to handle aggressive electrolytes.
2. Key Properties That Make Tantalum Wire Unbeatable
- Purity Matters: DTa1 wire limits impurities like Fe (<0.0045%) and Ni (<0.0025%) to prevent electrical leakage.
- Mechanical Strength: Hard-state wires (Y) achieve tensile strengths >1250 N/mm², resisting deformation.
- Low Leakage Current: ≤0.10 μA/cm² ensures capacitor stability (tested via GB/T 26012 Annex A).
- Surface Capacitance: 10–12 μF·V/cm² for liquid capacitors, crucial for energy density.
3. Reliability Testing
Before deploying Ta wire, rigorous tests are mandatory:
- Oxygen Embrittlement Test: Bend wires 3–6 times (based on diameter) without cracking.
- Straightness Check: Ensure arcs align with an 800 mm template to avoid assembly issues.
- Leakage Current Validation: Use 0.1% H₃PO₄ solution under 180V to measure μA/cm².
Case Study: A smartphone manufacturer reduced capacitor failures by 40% after switching to DTa2 wires with certified oxygen embrittlement resistance.
4. Applications
- Solid Capacitors: SDTa1 wires (0.1–0.2 mm) for compact devices like wearables.
- Liquid Capacitors: LDTa2 wires handle sulfuric acid electrolytes in power supplies.
- Aerospace: High-purity DTa1 resists radiation and thermal cycling in satellites.
Cost Tip: While tantalum costs more than copper, its 10x lifespan in harsh conditions lowers long-term expenses.
5. Choosing the Right Tantalum Wire – A Quick Checklist
- Define Your Environment:
- Corrosive fluids? Use doped DTa2.
- High temperatures? Opt for vacuum-melted grades.
- Verify Certifications: Ensure compliance with ASTM B521 or GB/T 26012.
- Partner with Experts: Work with suppliers offering mill test reports for traceability.
Conclusion: Elevate Your Capacitors with Certified Tantalum Wire
From medical devices to military tech, tantalum wire is the unsung hero ensuring reliability. By prioritizing grade purity, mechanical performance, and rigorous testing, you’ll avoid costly failures and boost product longevity.