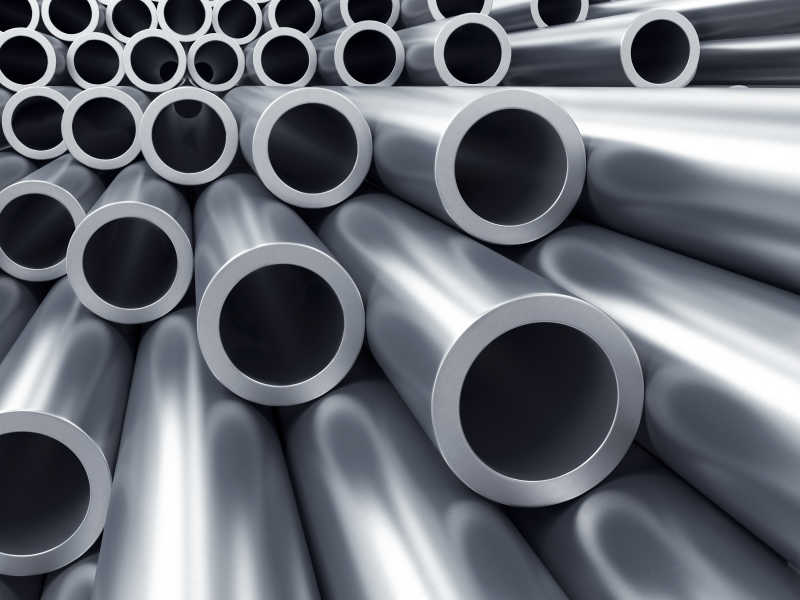
Why Tantalum Tubes Are Your Best Solution for Extreme Corrosion Resistance
Introduction: What Makes Tantalum Tubes Uniquely Durable?
If you’re designing equipment for corrosive environments—like chemical processing or semiconductor manufacturing—tantalum tubes are your go-to material. Certified under ASTM B521-22, these tubes combine unmatched corrosion resistance with mechanical strength. But how do you choose the right grade or type? Let’s break down the science and standards.
1. Understanding ASTM B521: The Gold Standard for Tantalum Tubing
The ASTM B521-22 specification defines requirements for seamless and welded tantalum tubes across five key grades:
- UNS R05200/R05400: Pure tantalum (vacuum-melted or powder-metallurgy).
- UNS R05252: Tantalum + 2.5% tungsten alloy (ideal for high-temperature stability).
- UNS R05255: Tantalum + 10% tungsten (extreme strength for aerospace).
- UNS R05240: Tantalum + 40% niobium (cost-effective for moderate corrosion).
Why This Matters for You:
- Each grade is optimized for specific industrial challenges.
- ASTM B521 ensures rigorous testing for leaks, cracks, and dimensional accuracy.
2. Seamless vs. Welded Tubes: Which Should You Choose?
Seamless Tantalum Tubes
- Made by extrusion or pilgering for zero weak points.
- Required for ultra-high-purity applications (e.g., semiconductor reactors).
- Pass flattening tests (no cracks under 20% diameter expansion).
Welded Tantalum Tubes
- Fabricated from rolled sheets via automatic argon arc welding (no filler).
- Cost-effective for large diameters (e.g., heat exchangers).
- Must pass reverse flattening tests to validate weld integrity.
Your Decision Checklist:
✅ Prioritize seamless tubes for high-pressure systems.
✅ Use welded tubes for non-critical, large-scale installations.
3. How ASTM B521 Ensures Your Tantalum Tubes Won’t Fail
Every tantalum tube under ASTM B521 undergoes strict quality checks:
- Hydrostatic Testing: Tubes withstand 75% of yield strength pressure (calculated as
P = 2St/D
). - Eddy Current/Ultrasonic Testing: Detects defects as small as 0.004-inch wall pits.
- Helium Leak Testing: Guarantees <10×10⁻⁷ cm³/s leakage for vacuum systems.
Real-World Example:
A semiconductor plant using R05252 tubes saw zero failures over 5 years, even in 130°C sulfuric acid.
4. 3 Critical Factors When Ordering Tantalum Tubes
- Grade Selection:
- Use R05255 (10% tungsten) for high-stress environments.
- Choose R05240 (tantalum-niobium) for budget-friendly nitric acid systems.
- Dimensional Tolerances:
- Diameter accuracy: ±0.004 inches for tubes <1 inch.
- Wall thickness variation: ≤10% for seamless pipes.
- Certification Requirements:
- Demand ASNT SNT-TC-1A-certified technicians for non-destructive testing.
5. Why Your Industry Relies on Tantalum Tubes
- Semiconductors: Ultra-pure R05200 tubes prevent contamination in etching baths.
- Pharmaceuticals: Welded tubes handle aggressive solvents like HCl.
- Oil & Gas: Seamless R05255 tubes survive sour gas (H₂S) environments.
Cost-Benefit Tip: While tantalum costs 5x more than stainless steel, its 50-year lifespan reduces total ownership costs by 300%.