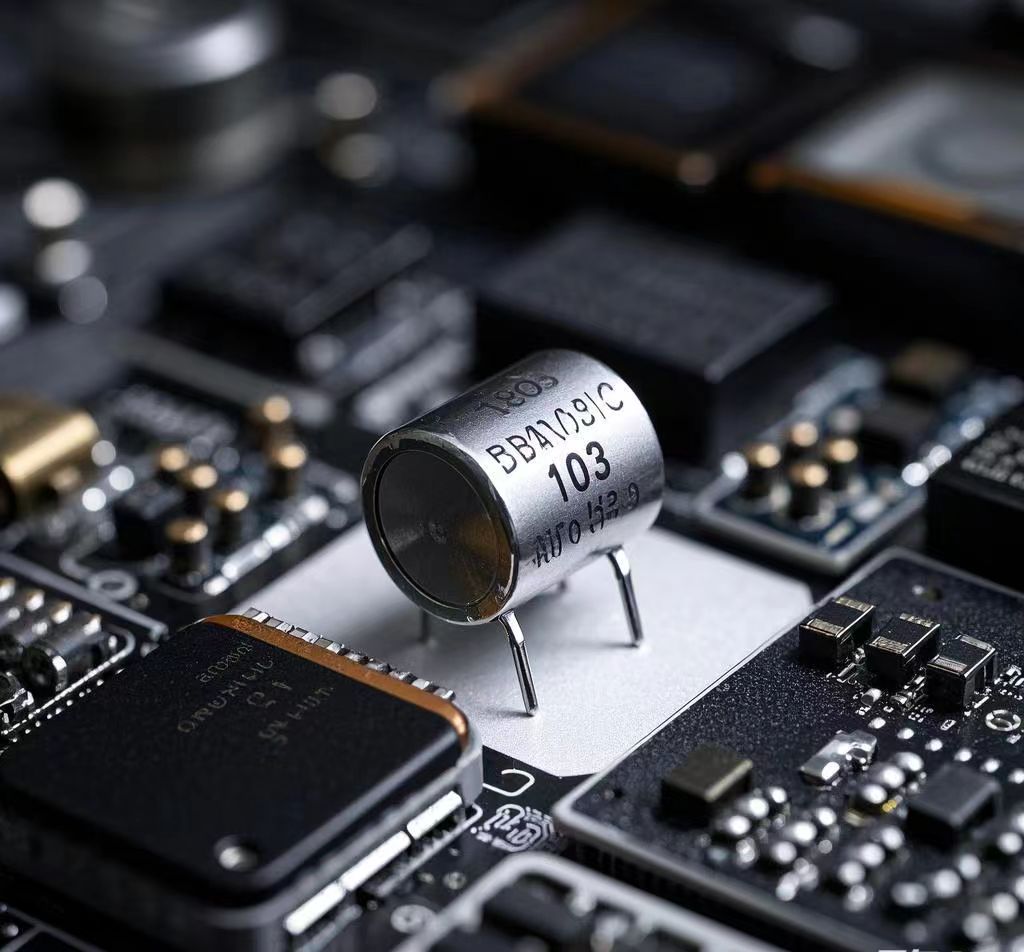
Tantalum capacitors are used to eliminate rust spots on tantalum wire so that tantalum capacitors can work efficiently on tantalum wire
If you’re manufacturing or sourcing tantalum capacitors, the quality of your tantalum wire directly impacts reliability. Surface rust spots on the wire can lead to capacitor failures, increased leakage current, and reduced lifespan. Let’s dive into why these defects occur and how to prevent them—backed by industrial research.
Why Rust Spots Threaten Your Tantalum Capacitors
Tantalum capacitors rely on ultra-pure tantalum wire to function efficiently. Rust spots—abnormal oxide or carbide formations (e.g., Ta₂O₅, TaC)—compromise the wire’s surface integrity. Here’s what happens:
- Leakage Current Surges: Defective wires increase leakage by 3–4x (from 0.0006 μA/mm² to 0.0023 μA/mm²).
- Mechanical Weakness: Rust spots reduce elongation by 27% and fracture resistance by 50%, making the wire brittle.
- Performance Failures: Capacitors with contaminated wire fail under high-temperature or high-voltage conditions.
How Rust Spots Form on Tantalum Wire
Based on the study, three root causes dominate:
1. Contamination During Processing
- Problem: Rolling, drawing, or cleaning introduces low-melting-point metals (Al, Ca, Na) via lubricants or molten salts.
- Result: These impurities react with oxygen/carbon during annealing, forming stubborn rust spots.
2. Surface Defects from Powder Metallurgy
- Problem: Powder-based sintering leaves micro-pores and cracks (see Fig. 9).
- Result: Defects trap contaminants, accelerating oxidation at high temperatures.
3. Poor Oxide Layer Control
- Problem: Uneven surface oxidation during salt bath treatment (e.g., using Na/Al salts).
- Result: Weak oxide layers flake off, exposing fresh tantalum to further corrosion.
3 Proven Strategies to Protect Your Tantalum Wire
1. Optimize Sintering & Rolling
- Action: Increase sintering temperature (2,600°C) and extend dwell time to reduce pores.
- Why It Works: Denser structures (Fig. 10) minimize defect sites for contamination.
2. Strict Process Monitoring
- Checkpoints:
- Rolling: Inspect for burrs, pits, or grooves post-rolling (use SEM analysis).
- Drawing: Replace worn dies to avoid surface scratches.
- Cleaning: Apply ultrasonic cleaning to remove residual salts (e.g., Na, Ca).
3. Enhance Surface Treatment
- Action: Use controlled molten salt baths with pure media to form uniform oxide layers.
- Avoid: Cross-contamination from low-purity salts (common culprits: Na, Al, Ba).
Critical Tests to Validate Your Tantalum Wire Quality
- SEM-EDS Analysis: Scan for oxygen/carbon spikes and trace metals (Fig. 2–5).
- Mechanical Testing: Ensure elongation ≥20% and fracture resistance ≥4 bends (Table 1).
- Leakage Current Check: Keep below 0.001 μA/mm² (industry standard).
Key Takeaways for Your Production Line
- Prevent > Cure: Rust spots are irreversible—focus on contamination control.
- Prioritize Density: Opt for high-purity tantalum powder and refined sintering.
- Partner Smartly: Collaborate with certified suppliers (e.g., Ningxia Orient Tantalum) for defect-free wire.
Need actionable solutions? Share your challenges below—let’s troubleshoot rust spots in tantalum wire and boost your tantalum capacitor reliability!
Reference: Xie Yongxu et al., “Study on the Formation Mechanism of Rust Point on the Surface of Capacitor-Grade Tantalum Wire,” Powder Metallurgy Industry (2022).