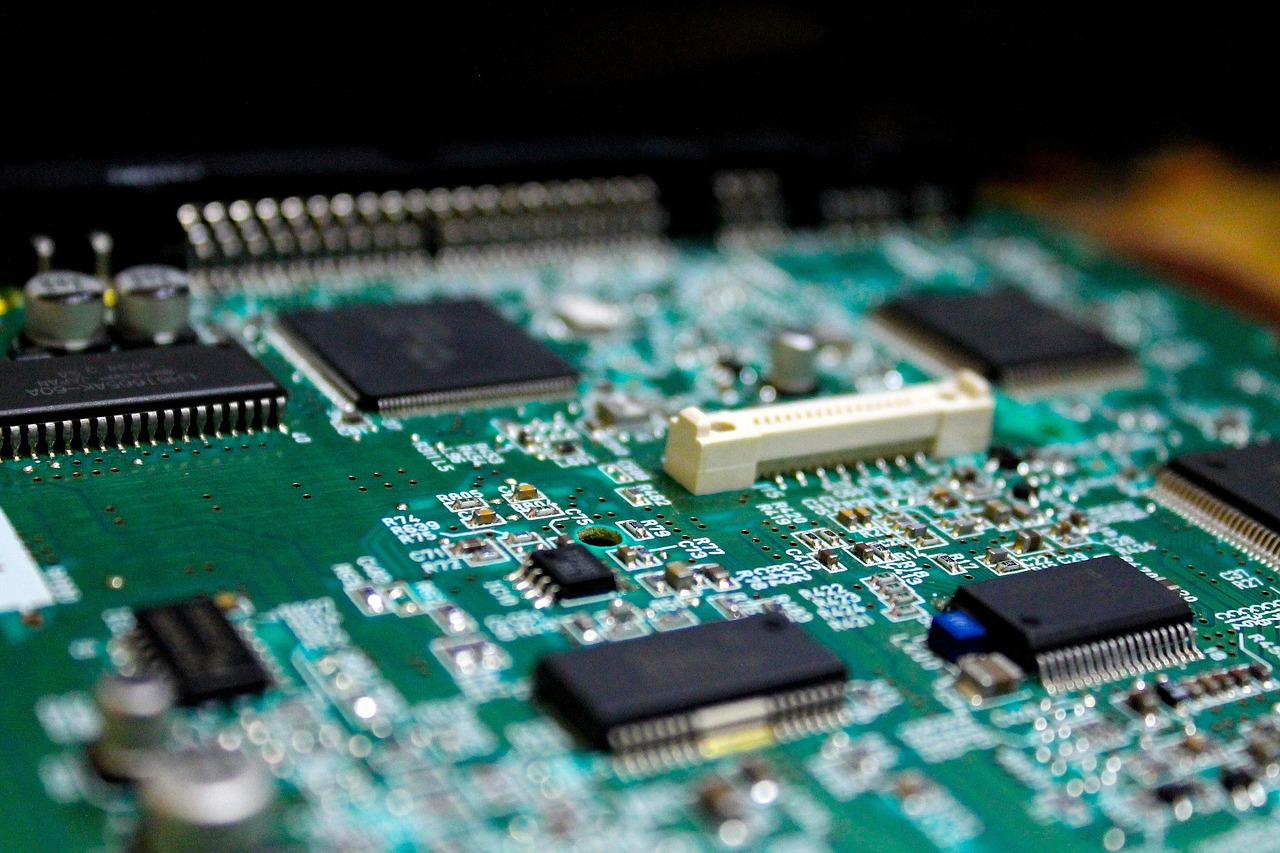
How You Can Optimize Tantalum Rod Preparation for Semiconductor Applications
How You Can Optimize Tantalum Rod Preparation for Semiconductor Applications
If you’re working with tantalum rods in semiconductor manufacturing, achieving precise hardness and grain size is critical for performance. Let’s break down a proven optimization strategy to elevate your tantalum rod quality—backed by industrial research.
Why Tantalum Rods Matter in Semiconductors
Tantalum rods serve as raw materials for magnetron sputtering rings, which are essential in depositing thin films onto silicon wafers during chip production. The rods must meet strict standards: hardness ≤130 HV and grain size finer than ASTM 8 to ensure uniformity and durability under high-energy particle bombardment.
Key Challenges in Conventional Processes
Traditional methods often produce rods with inconsistent grain sizes (ASTM 2.5–6.0) and uneven hardness. For semiconductor-grade quality, you need tighter control. Here’s how researchers tackled this:
Two Optimization Strategies Tested
The study compared two advanced workflows:
Option 1: Simplified Forging
Steps: Square forging → heat treatment → flattening → final rolling → post-heat treatment.
Results: Average hardness 117.1 HV, grain size ASTM 7.5–8.0.
Option 2: Multi-Stage Forging
Steps: Upsetting-drawing forging → heat treatment → flattening → secondary heat treatment → final rolling → post-heat treatment.
Results: Hardness 106.3 HV, grain size ASTM 8.0–8.5.
Why Option 2 Wins:
Achieves finer, more uniform grains (ASTM 8+).
Lower hardness ensures better machinability without compromising structural integrity.
Scalable for industrial production.
Critical Factors for Your Process Optimization
Controlled Forging: Multi-stage deformation (e.g., upsetting-drawing) refines grain structure.
Strategic Heat Treatment: Intermediate annealing prevents work hardening and balances hardness.
Post-Rolling Precision: Final rolling under optimized parameters ensures dimensional accuracy.
Actionable Takeaways for Your Workflow
Prioritize Grain Refinement: Target ASTM 8+ by integrating multi-step forging and heat treatment.
Monitor Hardness Closely: Keep HV ≤130 to avoid brittleness.
Validate with Testing: Use cross-sectional grain analysis (see Figure 1 in the study) and hardness mapping.
Final Thoughts
By adopting the “Upsetting-Drawing + Multi-Stage Heat Treatment” approach, you can produce tantalum rods that meet semiconductor standards while boosting yield and consistency. Whether you’re scaling up or refining lab processes, this method offers a reliable blueprint.
Pro Tip: Always cross-reference your results with ASTM E112 grain size standards and validate via industrial partnerships (like the National Tantalum & Niobium Research Center).
Based on the study “Technology Optimization Research on Preparation of Tantalum Strip Used for Semiconductor” by Ma Xiaowen et al. (2018).
Need deeper insights? Share your challenges in the comments—let’s discuss how to adapt these methods to your production line!